In a high-risk industry such as metalworking, it is concerning that over a quarter (28%) of metalworkers are worried about their safety at work.
Today’s global manufacturing landscape is a result of rapid change in the industry over the last decade, driven by events such as the Covid-19 pandemic and the introduction of new technologies that have transformed ways of working irrevocably. This has created an influx of new responsibilities to manage, however, health and safety remain a critical priority in sectors such as metalworking where improper machinery or equipment operation can cause life-changing injuries. An unsafe working environment and lack of health and safety training poses a significant threat to employee wellbeing and can also prove costly to the business.
At FEIN, we work closely with our customers and conduct detailed assessments of their working environments and challenges in order to best support them with safety and performance. However, to deepen our understanding we embarked on research this year to capture the current experiences of health and safety in metalworking across disciplines, experience levels and seniority.
We surveyed over 100 UK metalworking professionals, asking them a range of questions to understand their experiences of:
- How health and safety is approached within their organisations.
- How safe and comfortable they feel at work.
- The tools available to use in their role.
Company approach
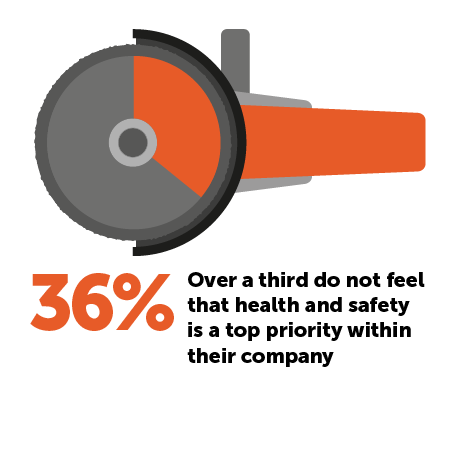
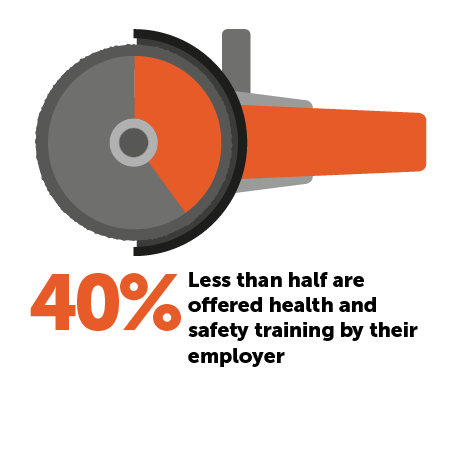
Our research revealed that the majority of metalworkers agree their safety is a top priority for employers, which reflects our own observations that particularly in the last few years, health and safety event engagement has increased. The Health and Safety Event in Birmingham this year was well attended and many visitors were keen to speak about the latest in safety developments to improve standards for their teams. However, we cannot ignore that 36% of respondents do not agree that health and safety is a top priority for their company.
The findings demonstrated a positive correlation between a respondent’s length of service in their sector and how likely they were to worry about their safety at work too. Metalworkers aged 55 or over (57%) and those having served in the sector for 20+ years (50%) were most likely to agree that they were worried about their safety. This is likely due to their longer service in the sector and the level of legislation and innovation change that has taken place in health and safety. These factors mean that they are more likely to have a heightened awareness of the risks involved in their role.
One of the easiest methods to implement to make employees feel safer and more comfortable at work is to conduct health and safety training, however, we found that less than half (40%) of those working in the metalworking sector are currently offered this. Those working at smaller companies are more likely to be missing out on this guidance, with only 13% of those working at companies with 1-9 employees agreeing that they had been offered training in health and safety. The same proportion of respondents in that company size category agreed that safety is a priority in their organisation. Whereas, 70% of employees at slightly larger companies (10-49 employees) are offered health and safety training and 70% of that group agreed that safety is a priority in their organisation. This highlights how impactful training can be for engaging employees and making the company commitment to safety standards clear.
Nathan Ford, Product Specialist at FEIN said “It really surprised us to see that less than half of the metalworkers we surveyed agreed that they are offered health and safety training. We firmly believe that health and safety training is a compulsory requirement for tool operators in the metalworking sector, and have witnessed the training that our customers carry out to ensure that machine operators are aware of the hazards associated with their role and working environment. However, there is always room for improvement and as new technologies continue to enter the landscape, we would encourage professionals to keep reviewing their policies and evolving their training methods in line with industry updates.”
Andy Mills, Managing Director at FEIN added “It’s great to see that the majority of metalworkers do feel that health and safety is a top priority within their company, and we have certainly seen this in the requests we receive for products with enhanced safety features. Since we launched our Protago cordless safety grinders, we have seen significant uptake from a huge variety of businesses who wanted to ensure the highest safety standards for grinder operators. However, we must not ignore that a third of metalworking professionals do not feel that their safety is a priority. Therefore, we must work with stakeholders at all levels to ensure that group discussions, training sessions and regular improvements are being made.”
Performance perceptions
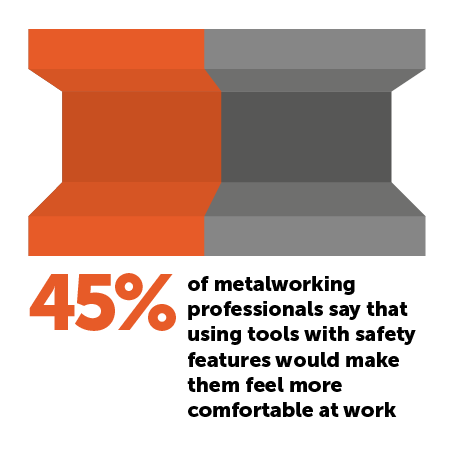
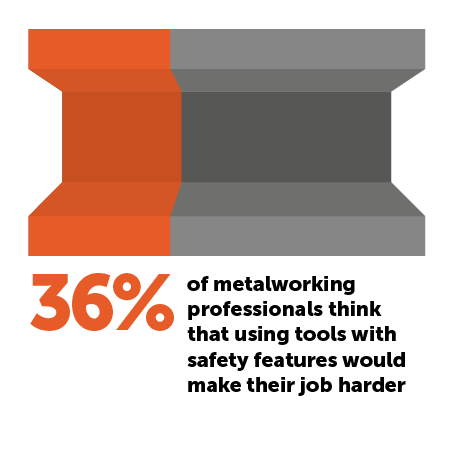
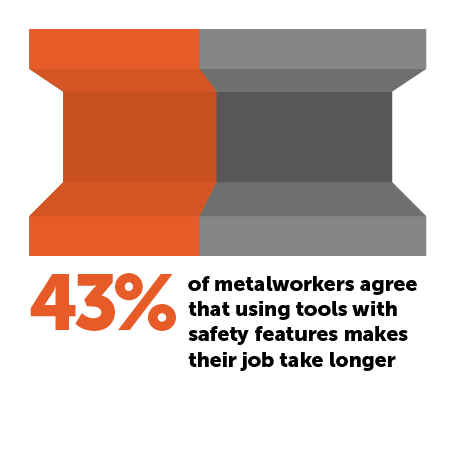
Our research uncovered that on the whole, metalworkers find safety features to be helpful rather than a hindrance. Over 30% of respondents did not agree that they can do their job safely with the tools currently provided, which highlights that there is still a gap between operator expectations and the features of the tools that they are currently purchasing or provided with.
We also explored the perception of safety features in the industry and why this may be the case, and found that a third (36%) of the metalworkers agree using tools with safety features makes their job harder. The responses, however, varied dramatically between job roles. 62% of fabrication managers agreed that safety features make the job harder, whereas only 29% of fabrication operatives felt the same way. This indicates that the adoption of safety tools could be hindered by traditional perceptions, rather than the tools that prioritise both safety and performance on the market today.
In addition to difficulty, we also investigated attitudes towards tools with safety features and the impact on the length of time it takes to complete a task. Whilst overall, 43% of metalworkers agree that using tools with safety features makes their job take longer, workshop, fabrication and operations managers were the most likely to agree, whereas only 29% of fabrication operatives felt the same way. This further demonstrates the difference in attitude between the roles, and how previous experiences can present a challenge to new product selection if conversations are not sparked across the industry to demonstrate the level of innovation for both safety and impact. Despite these perceptions, 45% of metalworking professionals agree that tools with safety features would make them feel more comfortable at work.
Nathan Ford at FEIN commented: “In regards to tool operation, there must be a balance between safety and productivity. Nobody should ever be working in an environment where safety comes second to delivery schedules. In the assessment of time vs safety, it is important to look at the whole process and not just one specific task. To illustrate how perceptions can restrict the uptake of safer tools, I had a customer who was using a punch type edge beveler which would process the edge in one pass, whereas our alternative would take three passes. He therefore thought it would take three times as long. However, looking at the HAV levels, their current tool could only be used for a maximum of 1hr 22mins, and ours could be used for 10hr 49mins before reaching the ELV limit. Overall, with our tool he could work for longer with less stress and less exposure to HAVs. Therefore, it is important to consider all of the factors in these decisions.”
Andy Mills at FEIN shared: “It may seem contradictory that almost half of metalworkers would feel more comfortable if they could use tools with safety features, and a similar proportion believe that such tools would make their jobs take longer. However, we know from speaking with customers that both beliefs are often held in the industry, where metalworkers do feel that safety features slow down their work, but it doesn’t mean that they don’t appreciate safety. What we need to produce as manufacturers are products which offer safety features which do not hinder work and if possible, can help increase productivity. Our new CG 15 grinders are a perfect example of this - many of the safety features do not make themselves known until they are needed. For example, the advanced kick back monitoring system will detect any sudden movement which is outside of the normal and switch the machine off. Under normal working conditions you would not even notice this but it has been implemented to protect the user’s safety.”
Safety features
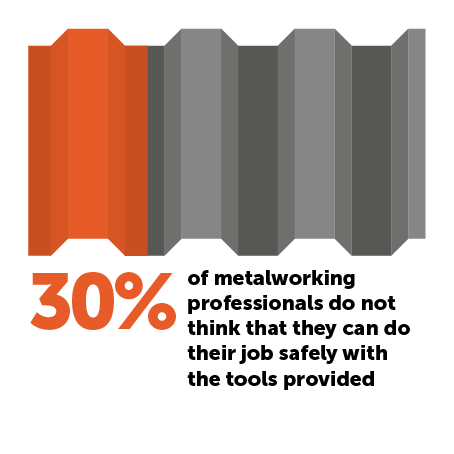
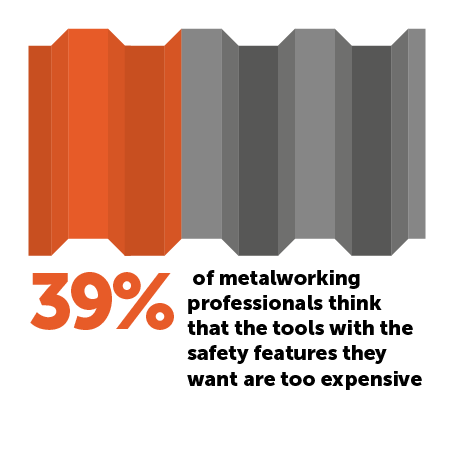
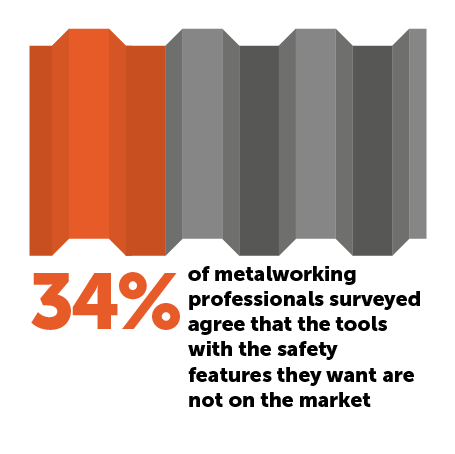
Despite the significant proportion of metalworkers who recognised that safety features could make them feel more comfortable at work, our survey revealed that 34% agree the tools with the features that they would want are not on the market. 50% of product managers agreed with that statement, in comparison to just 10% of HSE managers/officers. Unsurprisingly, HSE managers have a greater understanding of what is available on the market, however, they may need to collaborate more closely with the product managers to understand whether the safety-led tools that they have identified would be the best fit for the task in mind.
Whereas, 39% of metalworkers said that the tools with the safety features they want are too expensive, with operations managers (69%), product managers (50%) and workshop managers (46%) most likely to agree due to their purchasing responsibilities. Cost will undoubtedly be a factor in tool selection, particularly in light of the current economic situation, however decision makers must consider the total value of these tools. Upholding safety standards is critical for employee wellbeing and also the financial health of a business. Recent statistics show that workplace-related injury or ill health currently costs the UK economy an estimated £18.8 billion a year.
Nathan at FEIN shared: “We often hear from initial conversations with customers that the safety-led tools they want don’t exist. This is where the importance of working with tool manufacturers is so important. We can listen and learn from our end users, gaining a deeper understanding of their applications and what they need to make their job easier, and then set out to develop tools. Our recent project with Bouygues construction is a great example of what that collaboration can lead to. After numerous incidents on sites across Europe which involved the misuse of compact grinders, we worked with Bouygues and developed a product that has eliminated their concerns. We'd encourage users to contact manufacturers and discuss your needs so we can recommend suitable products.”
Andy at FEIN concluded “Across the industry, we see metalworkers navigating higher costs and deterred from exploring new safety solutions due to the price tag, however, these decisions should not be made without assessing the overall value. We are pleased to lead these conversations and demonstrate with real-life examples how investing in safety-led tools can dramatically improve safety standards – increasing confidence, reducing accidents and preventing expenses and downtime accrued in the event of injury.”
To discuss the research in more detail or for any questions, please contact us.