Why wear steel plate? Fab shops use hardened steel like Hardox AR400 and AR450 for its wear resistance, an advantage that makes what you build last longer. Hardox is approximately 5x harder than mild steel, a strength that is perfect for mining and excavation equipment fabrication. But working with that extreme strength also brings its share of challenges. A common question is - how do we drill it?
We have heard of many in-house drilling tricks but, for the most part, no one seams know how. In the end, the cutters get dull and you must replace them more often. Here is our technique, developed by our specialists to make your life easier.
Operation Requirement
- Variable speed mag drill
- Carbide annular cutter
- Cutting fluid
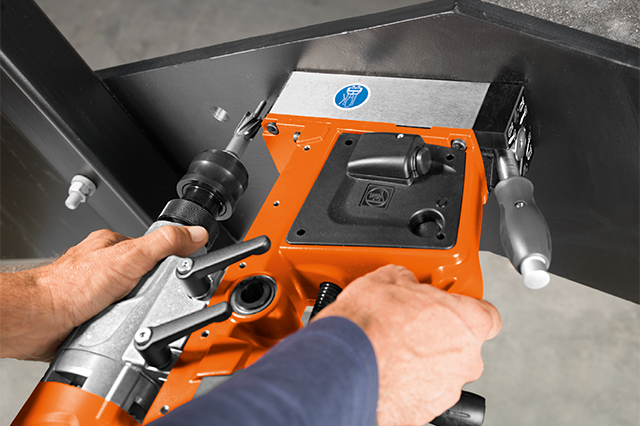
- Install a new carbide cutter.
- Position the mag drill.
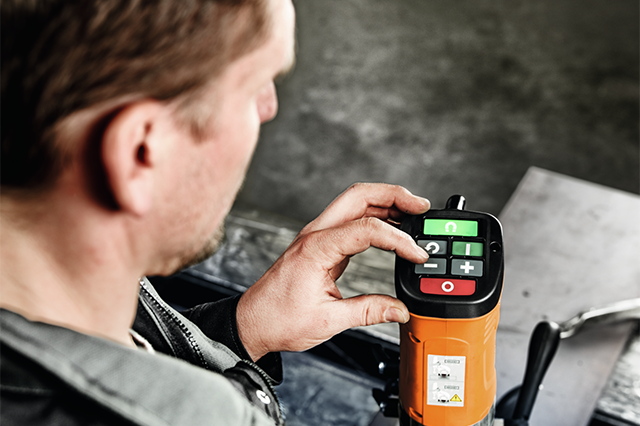
- Make sure your mag drill has variable speed control.
- Adjust the RPM to achieve the right cutting speed (see speed table for wear steel).
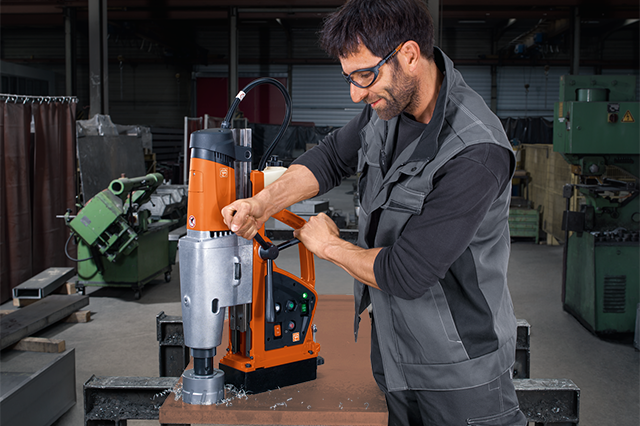
- Drill through the material in one continuous motion. Avoid stopping or moving backwards to break the chips.
- Use plenty of coolant lubricant. Open coolant valve to maximum flow and cool additionally from the outside.
Key elements for drilling in Hardox
- Always start with a brand new carbide cutter.
- Adjust the RPM to achieve the right cutting speed (see speed table HARDOX).
- Keep the distance between the cutter and the surface very tight.
- Use plenty of coolant lubricant. Open coolant valve to maximum flow and cool additionally from the outside.
- Do not press too hard during drilling.
- Drill through the material in one continuous motion. Don´t stop or move backwards to break the chips. HARDOX reacts with heat and can work-harden.
Wear Steel Recommended Speed Chart
Ø Imperial [in.]
1/2"
9/16"
5/8"
11/16"
3/4"
13/16"
7/8"
15/16"
1"
RPM AR 400
500
445
400
365
335
310
285
265
250
RPM AR 450
375
335
300
270
250
230
215
200
185
Click the button below to obtain a printable drilling speed chart from 1/2" to 4" and from 12mm to 100mm.