Stationary belt grinders are powerful and remove large amounts of material. However, they are comparatively large, usually require three-phase alternating current and are a major investment. What's more, the workpieces have to be taken to the tool before they can be machined. Angle grinders on the other hand are flexible and can be used for cutting or polishing as well as sanding jobs. But when used for challenging work, such as sanding welded seams, they run continually at maximum capacity. The contact face of the grinding disc is comparatively small so the abrasive quickly chokes or wears. Because angle grinders are guided freely, it's very hard to machine convex or concave shaped workpieces with precision.
For metal processing companies which often need to grind heavy workpieces or large areas, a hand-guided belt grinder is a flexible and low-cost alternative. Hand belt grinders deliver considerably better results. When grinding a welded seam, their 50 mm wide and 1 m long grinding belt allows them to remove around three times as much material as an angle grinder with a comparable abrasive. Weighing 5.6 kg, they are hardly any heavier than a large angle grinder and are easier to guide. Because the grinding belt is placed on the welded seam and guided along the seam with comparatively little pressure, they are very easy to use. Hand-guided belt grinders are used to prepare, chamfer and reliably remove any kind of welded seam. They are also used to grind radii, sand down rusty surfaces and create a satin finish. They are the convenient way to machine pipes and profiles too.
FEIN has two models for machining steel, stainless steel, casting and aluminium. They require single-phase alternating current and are operated with normal sockets. The GHB 15-50 hand-guided belt grinder has a power output of 1500 W and runs at a constant speed of 8500 rpm. The GHB 15-50 INOX hand-guided belt grinder with a controllable speed of between 2500 and 7900 rpm was designed especially for stainless steel processing. It is also suited for use with fleece belts and can machine stainless steel surfaces to a satin finish in a single step. Both tools can be converted into a stationary belt grinder using a table bracket attached at three points.
The motor can be rotated through almost 360 degrees to adapt to the prevailing circumstances. The front anti-vibration handle reduces vibration and can be adjusted into three different positions for ergonomic and flexible working. The grinding table is 80 mm long and a round recess makes it easier to machine pipes. The contact wheel with helical groove acts like teeth when grinding, thereby increasing the amount of material removed. The force is transferred with virtually no slip to the grinding belt by a drive wheel coated with polyurethane. Friction resistance is improved and the drive wheel's tool life is extended. A system patented by FEIN allows the grinding belt to be changed without the need for tools.
Tip:
For a very high sanding capacity and very long service life, FEIN has developed Cubitron precision grinding belts with ceramic grit (series C). Series R (green) was developed for extreme sanding work including jobs involving stainless and high-alloy steel. Series Z (blue) is the all-rounder for sanding and deburring steel and non-ferrous metals. Series A (red-brown) includes grinding belts with a fine grit for fine grinding metals to a final finish. The fleece belt conceals minor imperfections to produce the perfect finish.
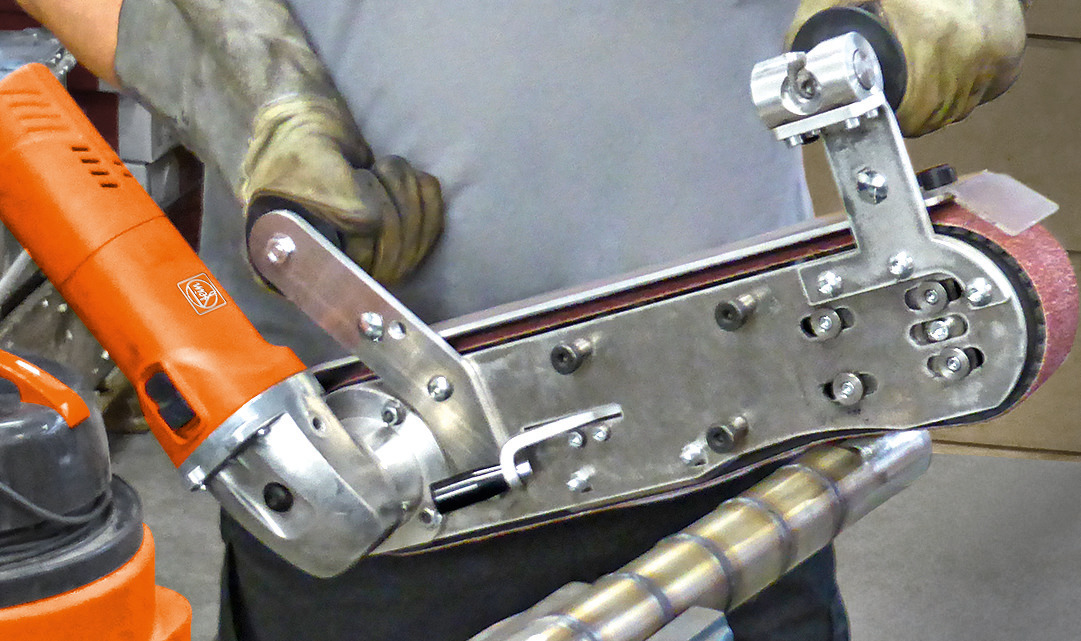